Introducing the Technology of Dehydrating Garlic Flakes
The dehydration technology used in our garlic flake production line ensures the production of dehydrated garlic flakes with a neat appearance, a slightly yellow hue, and a pure taste. This process involves dividing, peeling, washing, slicing, dehydrating, and drying the garlic, and finally sterilizing the dried flakes.
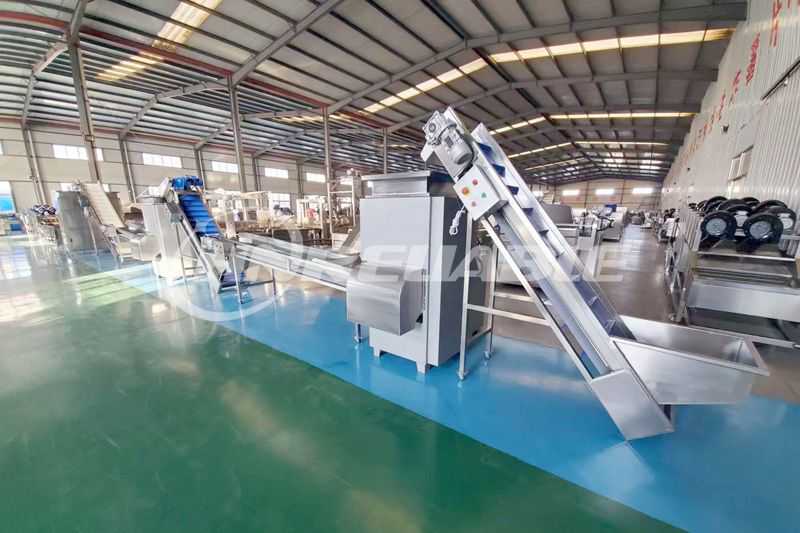
These dehydrated garlic flakes can be eaten directly or used as food raw and auxiliary materials. Rehydration is simple; just soak them in warm water. Available all year round, these flakes are a hot commodity in the market.
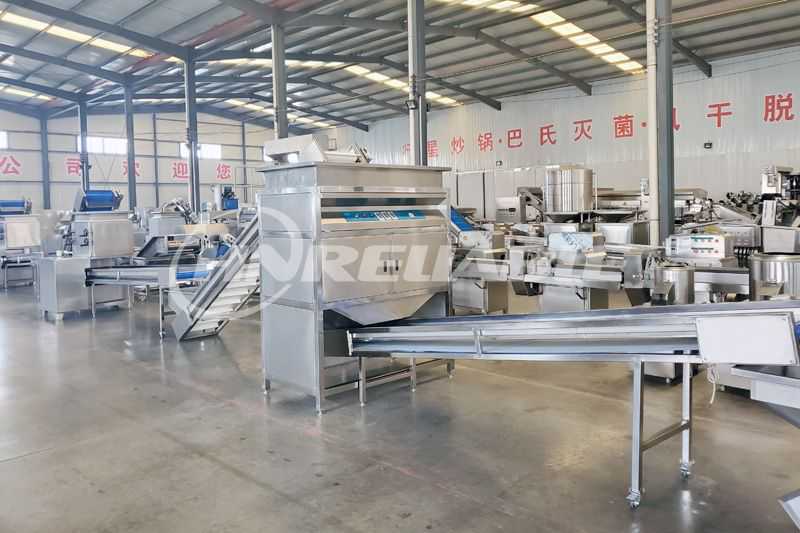
Importance of Garlic Flake Thickness in Dehydration Quality
Quality dehydration of garlic hinges critically on the thickness of the flakes. A smooth cut surface, uniform thickness, and appropriate size are the key factors to focus on. Ideally, the slice thickness should be around 1.5-2mm. Flakes that are too thick (e.g., 3mm) only retain about 70% of thiosulfinate, while flakes that are too thin (e.g., 1mm) have a higher fragmentation rate and less than 17% thiosulfinate retention. At the optimal thickness of 1.5-2mm, the color and appearance of dried garlic are excellent, and the retention rate of allicin is higher at 50-65%. Hence, adhering to the right thickness of garlic flakes guarantees the best efficiency, quality, and allicin content of dried garlic flakes.
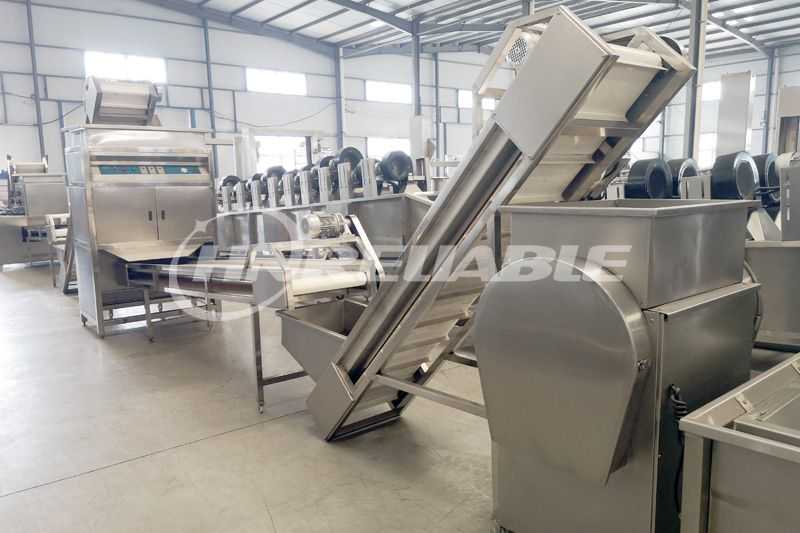
Understanding the Garlic Flakes Dehydration Processing Flow
The dehydration process of garlic flakes includes several steps: garlic splitting, garlic peeling, washing of peeled garlic, garlic slicing (or cutting), garlic blanching, de-watering of garlic flakes, dehydration of garlic flakes, and finally cooling, classifying, and packaging of dried garlic flakes.
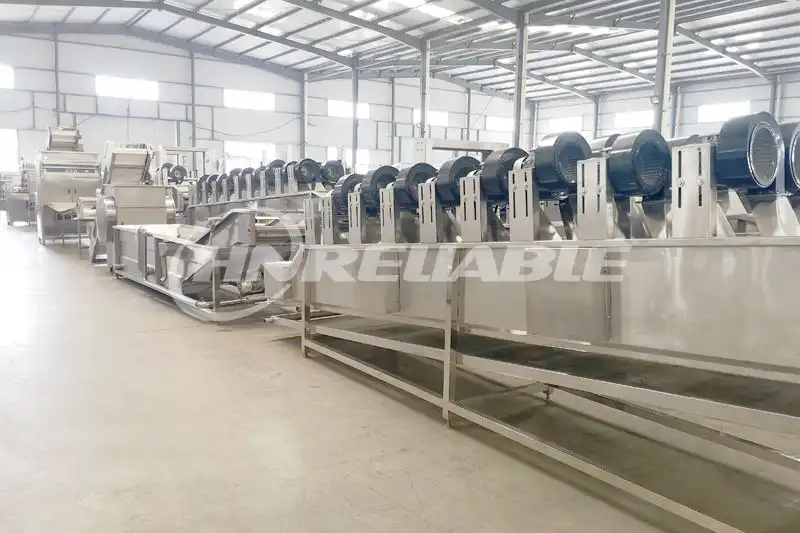
Dehydration Advantages of Garlic Flakes
Dehydrated garlic flakes are popular due to their neat appearance, slightly yellow color, and pure taste. They can be consumed directly or used as raw and auxiliary food materials. With the ability to rehydrate quickly in warm water, they offer the freshness of garlic all year round and are highly popular in the market.
Utilizing the Garlic Flakes Dehydration line
Our garlic flakes dehydration line boasts an aesthetically pleasing design, robust structural strength, stable material conveyance, and safe operation. The mesh belt type garlic flake dryer is equipped with an intelligent control system to provide the optimal drying environment for the garlic flakes at all times, thus ensuring a high-quality finished product.

Benefits of Garlic Dehydration
Garlic is known for its allicin content, about 2%, which exhibits wide-spectrum antibacterial and bactericidal effects. Allicin stimulates the formation of aromatic amino acids in animals, enhancing the aroma components in meat and eggs, making them more flavorful. Adding dehydrated garlic flakes to feed can improve the disease resistance of livestock, poultry, fish, and shrimp, and accelerate their growth rate. It has significant benefits in clearing plague, detoxifying, promoting blood circulation, and removing blood stasis.
Final Remarks on Garlic Flakes Dehydration
Dehydration ensures that the original flavor and nutrition of garlic are retained from splitting to dehydration. Apart from standard parts such as motors, radiators, bearings, and electrical components, the equipment is made of food-grade stainless steel. This makes it easy to clean and complies with the relevant national regulations on food hygiene.
FAQ
1. What is the process of dehydrating garlic flakes?
The dehydration process of garlic flakes includes several steps: garlic splitting, garlic peeling, washing of peeled garlic, garlic slicing (or cutting), garlic blanching, de-watering of garlic flakes, dehydration of garlic flakes, and finally cooling, classifying, and packaging of dried garlic flakes.
2. Why is the thickness of garlic flakes critical for dehydration quality?
The thickness of the garlic flakes plays a crucial role in maintaining the quality of the dehydration process. Flakes that are either too thin or too thick can affect the retention rate of thiosulfinate, a key compound in garlic. The optimal thickness for garlic flakes is around 1.5-2mm.
3. What is the ideal thickness of garlic flakes for the best dehydration results?
The ideal thickness of garlic flakes for optimal dehydration results is 1.5-2mm. This thickness ensures a good color and appearance of dried garlic, along with a higher retention rate of allicin at 50-65%.
4. How are the garlic flakes restored for use?
Dehydrated garlic flakes can be easily restored by soaking them in warm water, making them convenient to use all year round.
5. What are the advantages of dehydrated garlic flakes?
Dehydrated garlic flakes maintain the original flavor and nutrition of fresh garlic. They can be used directly in food or as raw and auxiliary materials. They're also easily restorable by soaking in warm water, offering the freshness of garlic in all seasons.
6. How does the garlic flakes dehydration plant ensure the quality of the finished product?
The garlic flakes dehydration plant uses an intelligent control system in its mesh belt type garlic flake dryer. This system maintains an optimal drying environment at all times, ensuring the best possible quality of the finished product.
7. What are the health benefits of dehydrated garlic?
Garlic contains about 2% allicin, which is known for its antibacterial and bactericidal properties. Allicin can stimulate the formation of aromatic amino acids in animals, enhancing the aroma in meat and eggs. In animal feed, it can improve disease resistance and accelerate growth rates.
8. What materials are used in the construction of the dehydration plant?
Except for standard parts like motors, radiators, bearings, and electrical components, the equipment in the dehydration plant is made of food-grade stainless steel. This ensures it's easy to clean and complies with national regulations on food hygiene.
9. What happens if the water content in the garlic flakes exceeds 6%?
If the water content in the garlic flakes exceeds 6%, they need to be baked again to ensure the correct dehydration level.
10. What is the color of properly dehydrated garlic flakes?
Properly dehydrated garlic flakes should have a slightly yellow color. They should be slightly yellow, large, complete, flat, uniform in thickness, without fragments, and without any peculiar smell.